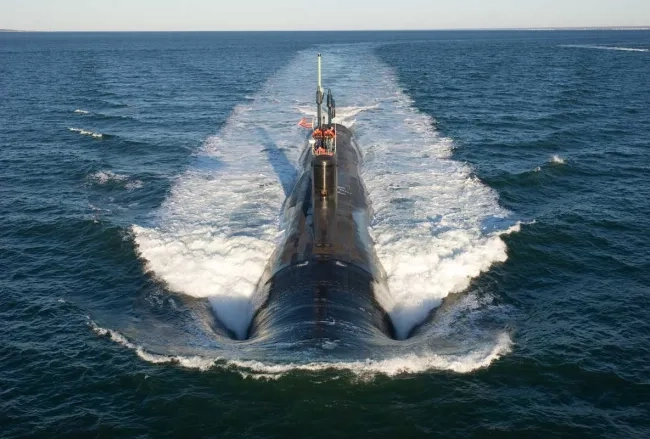
Hiring and retaining a robust workforce is the key challenge the submarine industrial base must overcome to reach the Navy's desired production rate of one Columbia- and two Virginia-class submarines each year, according to a senior official.
Speaking Wednesday at the Naval Submarine League Symposium, Executive Director of Strategic Submarines Matt Sermon said two recent industrial base studies performed by the Pentagon’s cost assessment and program evaluation office indicate the submarine industrial base is “gated by workforce.”
“Our ability to get the key technical trades, the engineering, the project management and leadership workforce to do ‘one plus two plus sustainment plus partnership’ is challenged,” Sermon said, referring to the Navy’s goal of building and maintaining its own submarines in addition to selling vessels to Australia under the AUKUS security partnership.
“That's why you heard in my discussion today, as well as in my everyday actions, that focus on connecting with the nation. Attraction, recruiting, training, retention is our foundational item,” he continued.
Over the next decade, the submarine industrial base will need to hire at least 100,000 skilled workers to support new submarine construction alone, Sermon said, with the total number of required new personnel exceeding 140,000 when accounting for sustainment needs on top of production.
“We're actually assessing the data because I think the numbers are a little higher, but over the next 10 years we have to hire 100,000 workers into the submarine industrial base on the new construction side,” he told reporters.
“I think that number is a little higher especially as we come to grips with post-COVID normal attrition,” he continued. “We’ve got to get better on attrition but as we come to grips with that model, it’s probably a little higher than 100,000. The sustainment numbers are high too.”
To address hiring and retention challenges, the Navy has turned to a non-profit company called Blue Forge Alliance, contracted through shipbuilder General Dynamics Electric Boat. The company received over $200 million in government funding across fiscal year 2023 to implement workforce development initiatives, Sermon told reporters.
Blue Forge Alliance’s work aims to provide a unified industrial base development strategy across shipbuilders, suppliers and other businesses, Sermon said. The organization has played a leading role in developing the online recruiting website buildsubmarines.com and other advertising campaigns that aim to attract new candidates to shipbuilders and suppliers.
The goal of these initiatives, Sermon said, is to persuade a “larger market share” of recent graduates, workers currently employed in the service industry and veterans transitioning into the civilian workforce to apply for jobs in the shipbuilding industry.
Expanding the use of new technologies, especially metallic additive manufacturing, can also enhance shipbuilding and sustainment, he continued.
Recently, the Navy used additive manufacturing to produce a submarine valve that the supply chain would have overwise been unable to deliver until 2025, he explained, saying the Navy plans to use this process to produce 100 critical submarine parts in the coming year to reduce maintenance cannibalizations.
The Navy is also working to improve the performance and retention rates of new industrial base employees by increase the number of new hires who go through official training pipelines like the Accelerated Training in Defense Manufacturing Program in Danville, VA.
“Those folks who go through the pipelines -- the shipbuilders and the suppliers and the talent pipelines -- have a much higher retention rate and they advance more quickly,” Sermon said. “So, focusing on getting the capacity of those pipelines to the right level, recruiting people into those pipelines and making a larger percentage of our incoming workforce those folks is crucially important.”